The National Cranberry Cooperative, or NCC, is a cooperative used in the Harvard Business School case study “National Cranberry Cooperative” in 1996.
The case study examines the problems faced by the cooperative in the past, specifically in the late 1960s, and how they were resolved.
- Challenges Faced by NCC and the Solution to Them
- 1) Peak Harvest Season Bottleneck
- 2) Inefficient Operations and Process Flow
- 3) Lack of Communication and Coordination
- 4) Quality Control Issues
- 5) Inaccurate Forecasting and Planning
- 6) Labor Constraints and Availability
- 7) Inadequate Storage and Warehousing
- 8) Transportation and Logistics Issues
- 9) Financial Management and Capital Investment
- Bottom Lines
Challenges Faced by NCC and the Solution to Them
Here, we have discussed the problems that the national cranberry cooperative faced in the beginning and solutions that the company applied to get out of the problems.
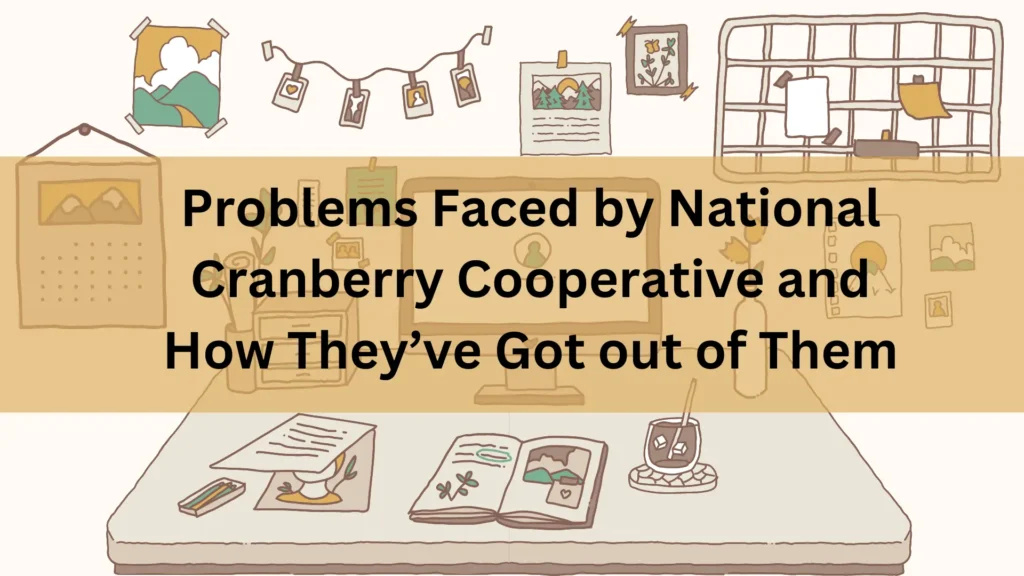
To get the details of NCC problems, you need to read the national cranberry cooperative case solution where you will get answers to all your questions.
You will get to know about the process of water harvested berries, bottleneck processing, trucks waiting issues, and installation of new driers etc.
However, we are here going to talk about this topic and discuss each of the problems briefly.
1) Peak Harvest Season Bottleneck
The NCC faced a significant bottleneck during the peak harvest season when cranberries had to be processed quickly.
This resulted in long waiting times for trucks delivering cranberries, as well as delays in unloading and processing. The cooperative struggled to handle the surge in cranberry supply.
Solution:
To address this issue, the NCC introduced a system of pre-harvest orders and staggered deliveries. This helped in spreading out the deliveries over a longer period, reducing the peak load during the harvest season.
2) Inefficient Operations and Process Flow
The cooperative had an inefficient process flow, leading to delays, congestion, and reduced throughput. The processes were not well-coordinated, causing idle time and increased handling of cranberries.
Solution:
The NCC implemented several operational changes, including the introduction of a “wet” and “dry” method for processing cranberries, mechanization of certain tasks, and redesigning the layout of the processing plant to streamline the flow of cranberries. These changes improved efficiency and increased throughput.
3) Lack of Communication and Coordination
There was a lack of effective communication and coordination among various stakeholders involved in the cranberry harvesting and processing operations. This resulted in confusion, delays, and inefficiencies.
Solution:
The NCC established a system for improved communication and coordination among cranberry growers, truckers, and plant personnel.
This included setting up a central control room to monitor operations, implementing a radio-based communication system, and creating standard operating procedures to ensure clear instructions and minimize misunderstandings.
4) Quality Control Issues
The cooperative faced challenges in maintaining consistent quality standards for cranberries due to variations in harvesting and processing practices.
Solution:
The NCC introduced quality control measures, such as establishing quality standards for cranberries, providing feedback to growers to improve harvesting practices, and implementing inspection processes to ensure adherence to quality standards.
5) Inaccurate Forecasting and Planning
The NCC encountered difficulties in accurately forecasting the cranberry supply and planning the processing operations accordingly.
This led to inadequacies, as the cooperative often faced either excess capacity or insufficient resources to handle the harvest.
Solution:
To address this issue, the NCC implemented a more sophisticated forecasting and planning system. They gathered data on historical harvest patterns, weather conditions, and grower projections to develop more accurate forecasts.
This enabled them to better allocate resources and plan for the upcoming harvest season, reducing waste and optimizing operations.
6) Labor Constraints and Availability
During peak harvest season, the NCC faced challenges in securing an adequate workforce to handle the increased workload. Labor shortages resulted in delays and disruptions in the processing operations.
Solution:
The cooperative implemented strategies to attract and retain seasonal labor. They improved working conditions, offered competitive wages, and provided training to ensure efficiency and productivity.
Additionally, the NCC explored partnerships with local labor agencies to source additional workers during the peak season.
7) Inadequate Storage and Warehousing
The NCC struggled with limited storage and warehousing facilities to accommodate the harvested cranberries. This led to congestion, increased handling, and potential spoilage of cranberries.
Solution:
To overcome the storage challenges, the cooperative invested in expanding their storage capacity and implementing better warehousing practices.
They constructed additional storage facilities and implemented a system for efficient cranberry handling, stacking, and preservation to minimize waste and maintain product quality.
8) Transportation and Logistics Issues
The NCC faced logistical challenges in transporting cranberries from the growers’ fields to the processing plant.
Insufficient transportation capacity, inadequate infrastructure, and poor coordination resulted in delays and increased transportation costs.
Solution:
The cooperative worked on improving transportation and logistics by collaborating with trucking companies and implementing a scheduling system for efficient delivery of cranberries.
They also explored options for infrastructure improvements, such as upgrading roadways and optimizing routes, to reduce transportation bottlenecks.
9) Financial Management and Capital Investment
The NCC encountered financial constraints and challenges in making necessary capital investments to modernize their operations and improve efficiency.
Solution:
To address financial issues, the cooperative sought external financing options and engaged in strategic partnerships. They secured loans for capital investment, allowing them to upgrade their equipment and facilities.
Additionally, the NCC explored collaborations with other stakeholders in the cranberry industry to share costs and leverage resources.
Bottom Lines
By tackling these problems and implementing appropriate solutions, the NCC was able to transform its operations and overcome the challenges that were hindering its efficiency and profitability.
The cooperative’s proactive approach in addressing these issues and continuously improving its processes contributed to its long-term success and sustainability.
These changes helped the cooperative overcome the challenges and operate more effectively and profitably.
It’s important to note that the case study was based on the NCC’s historical challenges and solutions, and it does not reflect the current or ongoing operations of any real cranberry cooperatives.